-
Impulses
- Impulses overview
-
Transformer manufacturers
- South America's champions of the energy transition
- Traction Transformers – Future on the Rail
- Time of the giants: XXL transformers for more power
- "Reinhausen is ready to deliver!"
- Oversized de-energized tap-changers
- The most powerful transformers in the world for a 1,100 kV HVDC line in China
- "We are in a growth market with the VRDT"
- Digitalization turnaround: GANZ Intelligent Solutions relies on cooperation with MR
- "Transitioning to a solution provider presents a major opportunity for transformer manufacturers – and digitalization can help!"
-
Digitalization
- How AI can lend a hand
- myReinhausen: MR's central digital customer platform
- Why data centers (may) never fail
- Automation? (Cyber-) Secure!
- Globally unique: MESSKO® MTRAB® dehydrating breather communicates via cell phone app
- Remote Solutions: Professional help from a distance
- "Digitalization of the power grids will only work with comprehensive security measures"
- Why are you digitizing your transformers? Three questions for Rúnar Svavar Svavarsson.
- Six challenges, six solutions – Intelligent sensors for safe transformers
-
Energy transition
- The VRDT is the ideal solution to solve voltage problems in our distribution grids
- Making transformers more sustainable
- 940 tons of power regulation
- Sunny prospects: Municipal solar storage devices
- Four reasons why regulated distribution grids are the future
- "The energy transition is taking place in the distribution grids"
- Five theses on the future of power grids
- Storage at all network levels
- Test systems for the energy revolution
- Climate change, energy revolution and the future of power grids?
- A new design for utility poles
-
Wind and solar power
- The North Sea as Europe's green power plant
- Sahara electricity - safe for the island
- Are wind farms the new power plants?
- Direct current at all grid levels
- The MSCDN plant – the new "power plant generator" for stable grids
- Clean power grid with high-frequency filters
- Weatherproof cable testing for offshore wind parks
- VRDTs for Australia's distribution grids
- Lifetime optimization
- Power supply in industry
- Globalization
- Impulses overview
-
Transformer manufacturers
- South America's champions of the energy transition
- Traction Transformers – Future on the Rail
- Time of the giants: XXL transformers for more power
- "Reinhausen is ready to deliver!"
- Oversized de-energized tap-changers
- The most powerful transformers in the world for a 1,100 kV HVDC line in China
- "We are in a growth market with the VRDT"
- Digitalization turnaround: GANZ Intelligent Solutions relies on cooperation with MR
- "Transitioning to a solution provider presents a major opportunity for transformer manufacturers – and digitalization can help!"
-
Digitalization
- How AI can lend a hand
- myReinhausen: MR's central digital customer platform
- Why data centers (may) never fail
- Automation? (Cyber-) Secure!
- Globally unique: MESSKO® MTRAB® dehydrating breather communicates via cell phone app
- Remote Solutions: Professional help from a distance
- "Digitalization of the power grids will only work with comprehensive security measures"
- Why are you digitizing your transformers? Three questions for Rúnar Svavar Svavarsson.
- Six challenges, six solutions – Intelligent sensors for safe transformers
-
Energy transition
- The VRDT is the ideal solution to solve voltage problems in our distribution grids
- Making transformers more sustainable
- 940 tons of power regulation
- Sunny prospects: Municipal solar storage devices
- Four reasons why regulated distribution grids are the future
- "The energy transition is taking place in the distribution grids"
- Five theses on the future of power grids
- Storage at all network levels
- Test systems for the energy revolution
- Climate change, energy revolution and the future of power grids?
- A new design for utility poles
-
Wind and solar power
- The North Sea as Europe's green power plant
- Sahara electricity - safe for the island
- Are wind farms the new power plants?
- Direct current at all grid levels
- The MSCDN plant – the new "power plant generator" for stable grids
- Clean power grid with high-frequency filters
- Weatherproof cable testing for offshore wind parks
- VRDTs for Australia's distribution grids
-
Lifetime optimization
-
Power supply in industry
-
Globalization
- Portfolio
-
Career
-
Company
404
Unfortunately,
this page no longer exists.
Maybe you made a spelling mistake or there was another problem.
If you still can't find anything, be glad to contact us.
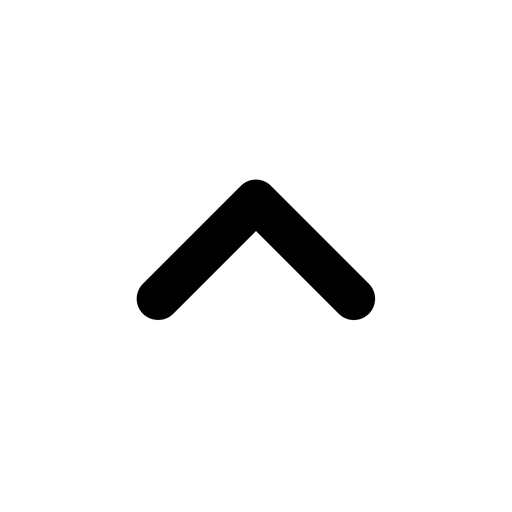
Contact
myReinhausen
We are here for you. Wherever you are.
Looking for the right contact partner?
Do you have a concern, but don't know whom you should contact? You will find that information in our contact overview. In the event of any technical disturbances, our 24/7 support is always at your disposal.
Welcome to myReinhausen
myReinhausen is MR's central, digital customer platform. On myReinhausen, customers can access customer-specific MR information as well as numerous free features related to the MR portfolio.
myReinhausenJoin Reinhausen family
Find your ideal job quickly!
Check our vacancies here. Apply today and contribute at the world market leader in energy technology keeping the energy supply stable in the future.